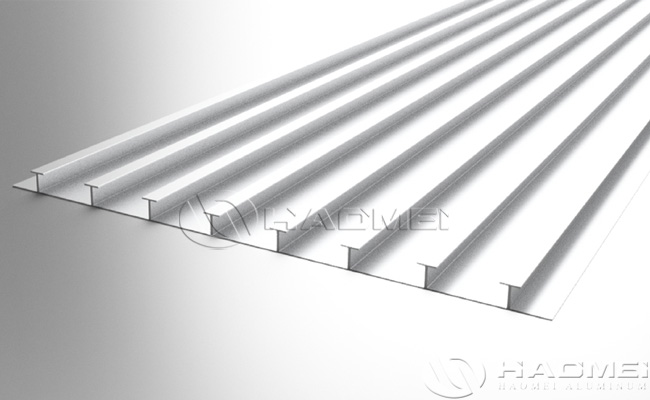
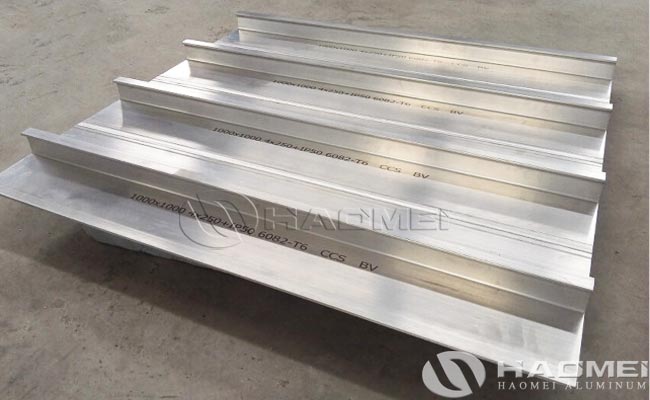
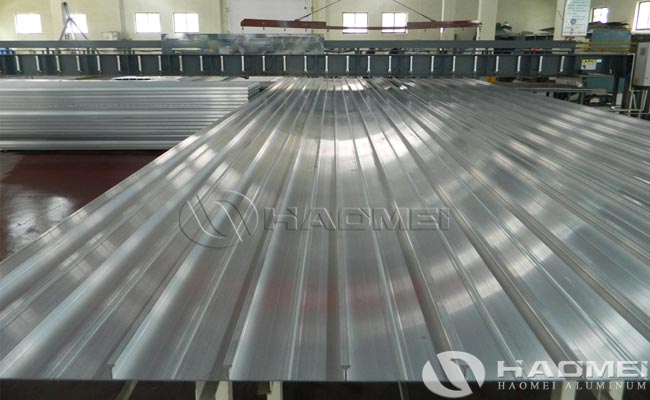
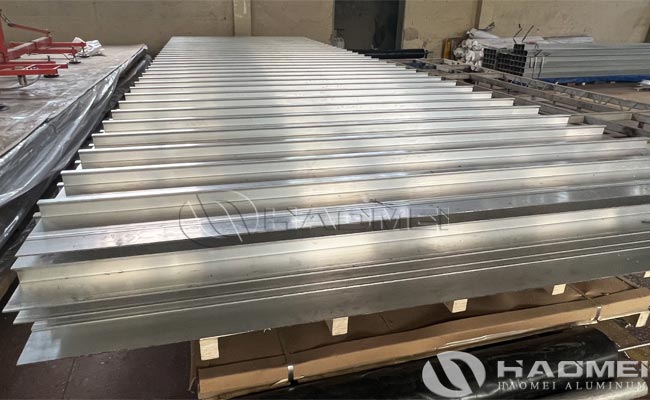
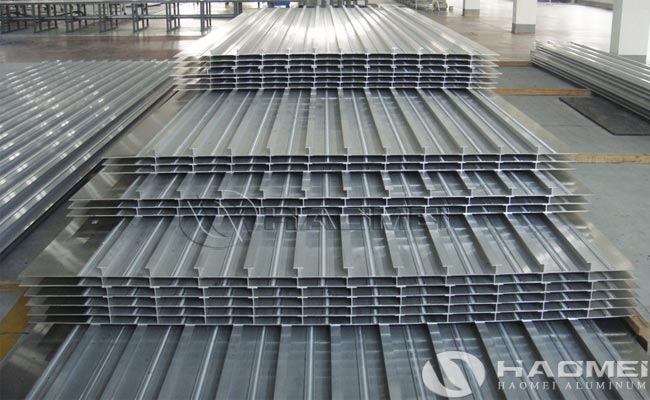
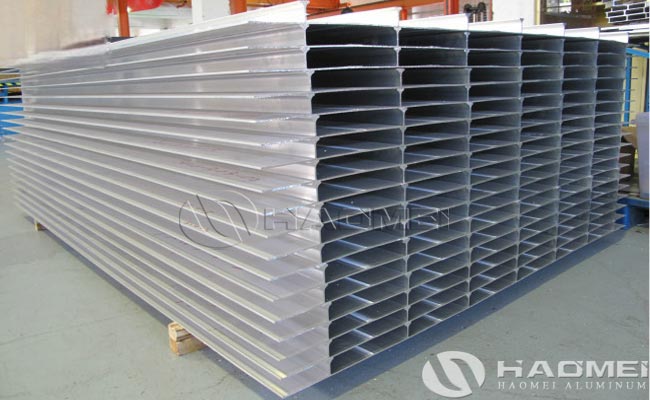
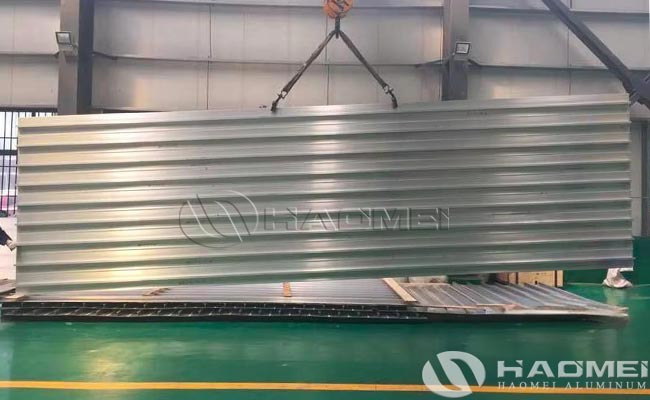
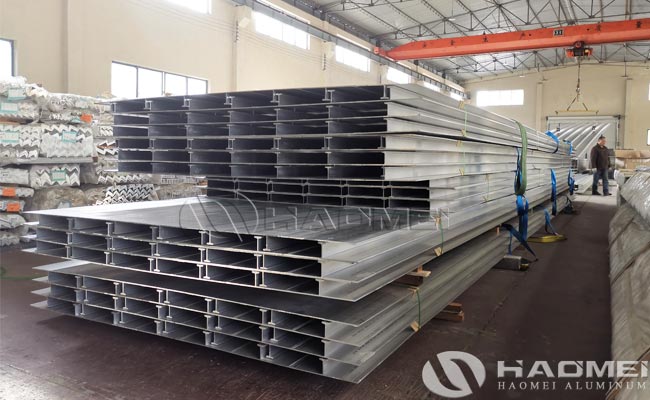
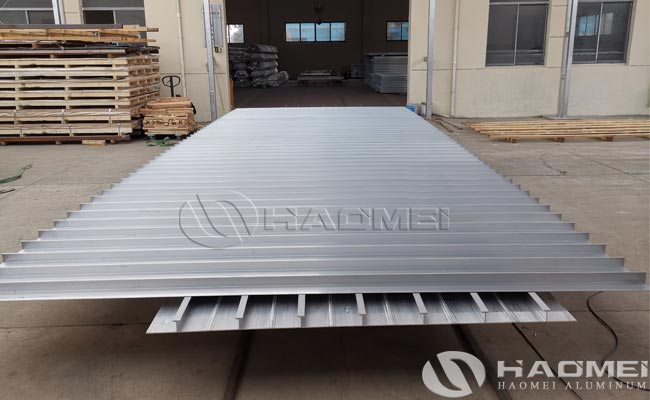
Friction Stir Welding Panel
- Product: Friction Stir Welding Plate
- Alloy: 6082
- Temper: T6
- Ribs: Single, Double, Multi ribs
- Application: Roof, wall, deck and other structure parts
- Ceritification: DNV, CCS, BV, LR, RINA, ABS
- Introduction
- Feature
- Application
- Pictures
- Video
- Download
The wide aluminum friction stir welding plate is a ribbed plate with a specific rib section shape made by a high-power extruder through an extrusion process, and then several ribbon plates are welded into a wide rib plate of length and width required by the designer through friction stir welding.
This wide ribbed friction stir welding plate replaces the conventional plate structure where reinforcement ribs and aluminum alloy plates are welded into an integral plate structure using molten argon arc.
The structural design of wide aluminum alloy friction stir welding rib plate not only meets the requirements of relevant specifications of China Classification Society, but also saves a lot of aluminum alloy welding wire and welding workload, shortens the ship construction cycle, and more importantly, it avoids welding deformation caused by argon arc melt welding, improves the aesthetics of the hull appearance and the construction quality of the ship. It has been widely used in the design and construction of aluminum alloy ships.
Why FSW is Applied in Shipbuilding?
Friction stir welding (FSW) is very suitable for both small and large shipbuilding projects because it can help you reduce assembly time or speed up the construction process.
FSW is a solution to the many problems have been facing with welding aluminum such as high distortion and poor weld quality. The flatness of the FSW panels, free from distortions and buckling will ensure the highest efficiency during fabrication and this will save man-hours/cost and improve quality.
Friction Stir Welding Principle and Microstructure:
The marine industry has made a rapid conversion to aluminum friction stir extrusions and was one of the first industries to utilize friction stir welding for commercial applications.
FSW, in the marine industry, is generally used to join multiple sheets of metal together to form large panels.
Applicaion of FSW in Marine Industry:
The FSW panel are applied to both the superstructure and hull of ships. The FSW panel product offered by Haomei Aluminum has been approved by all major classification societies such as DNV, CCS, BV, LR, RINA, ABS.
Specification of Aluminum Alloy FSW Panel:
Haomei Aluminum's highly automated FSW machine makes it possible to weld large size and wide span friction stir welding panels up to 15 meters in length.
The marine grade aluminum alloys we use are seawater resistant and have the mechanical properties of mild steel at merely one third of the weight.
Single stiffener panel | |||||
T1 | T2 | W | H | L | Grades |
(mm) | (mm) | (mm) | (mm) | (mm) | |
2.8 | 1.8 | 200 | 60 | 12500 | 6082-T6 |
4 | 3 | 250 | 43 | 12500 | 6082-T6 |
300 | 43 | 6082-T6 | |||
400 | 43 | 6082-T6 | |||
5 | 4 | 250 | 64 | 12500 | 6082-T6 |
300 | 54 | 6082-T6 | |||
6 | 5 | 250 | 55 | 12500 | 6082-T6 |
300 | 55 | 6082-T6 | |||
7 | 6 | 250 | 56 | 12500 | 6082-T6 |
300 | 66 | 6082-T6 | |||
8 | 7 | 250 | 57 | 12500 | 6082-T6 |
300 | 67 | 6082-T6 | |||
9 | 8 | 250 | 68 | 12500 | 6082-T6 |
300 | 68 | 6082-T6 | |||
9.6 | 9 | 250 | 59 | 12500 | 6082-T6 |
Double-stiffened panel | ||||||
T1 | T2 | W | H | P | L | Grades |
(mm) | (mm) | (mm) | (mm) | (mm) | (mm) | |
3 | 1.9 | 212 | 32.5 | 106 | 12500 | 6082-T6 |
2 | 270 | 37 | 135 | 6082-T6 | ||
3.5 | 2.5 | 270 | 37.5 | 135 | 12500 | 6082-T6 |
4 | 3 | 252 | 33 | 126 | 12500 | 6082-T6 |
320 | 38 | 160 | 6082-T6 |
Multi stiffened panel | ||||||
T1 | T2 | W | H | P | L | Grades |
(mm) | (mm) | (mm) | (mm) | (mm) | (mm) | |
3.5 | 2.5 | 345 | 37.5 | 115 | 12500 | 6082-T6 |
Note: The solutions we offer can be tailor made to suit the customer's requirements.
Facotry Equipment and Stock:
The marine aluminum plates are produced by Friction Stir Welding of large aluminium profiles, rather than the more traditional methods based on manual welding of sheet metal. The absence of melting during welding gives a modularised panel free from thermal distortions, and with a plane and smooth top surface. There is no need for after work such as grinding and brushing on friction stir welded panels. This results in a process that is cheaper overall with substantial weight reductions and an end product with a superior finish.
Packaigng and Load of Haomei Friction Stir Welding Plate:
Why Choose Haomei Aluminum?
- Specialization: We excel in providing top-grade marine grade aluminum profiles.
- Diverse Options: Explore a variety of other grades to suit your specific project requirements.
- Value-added Services: Benefit from efficient sourcing, quick turnaround, and services like precision saw cutting for seamless project integration.
- Reliability: As your trusted aluminum profile distributor, we are committed to meeting your needs promptly and efficiently.
- Certified: Haomei Aluminum is an ISO-certified, CCS,DNV, LR, KR, BV, RINA, and ABS cerificated, family-owned, and operated provider of high-quality specialty metals and alloys.
The advantages of Friction Stir Welding (FSW) Panel:
1. Cost Efficiency: While manufacturers may hesitate to disclose specific savings, the overall reduction in costs is significant. This is achieved through either investing in FSW facilities or sourcing prefabricated panels from specialized suppliers.
2. Reduced Distortion: FSW minimizes the thermal distortion often associated with traditional welding methods, resulting in more precise and uniform joints.
3. Single Pass Capability: In many cases, a single FSW pass can replace multiple MIG welding passes, particularly for thicker materials, thereby streamlining the manufacturing process.
4. Clean Joints: FSW produces no weld spatter, leading to clean surfaces and roots of joints. This high cosmetic quality can eliminate the need for additional finishing processes, such as painting, further reducing costs.
5. Health and Safety Compliance: The absence of weld fume during the manufacturing process aligns with tightening health and safety standards, making FSW a safer option for workers.
6. Flexible Orientation: FSW can be performed in any orientation, as gravity does not affect the process, allowing for greater versatility in manufacturing setups.
7. Energy Efficiency: The process is energy-efficient, contributing to lower overall operational costs.
8. Reduced Consumables: Unlike traditional welding methods, FSW does not require consumables like gas or filler wire, further enhancing cost-effectiveness.
9. Porosity-Free Welds: The welding process produces joints without porosity, which can enhance the integrity and reliability of the final product.
10. Excellent Mechanical Properties: FSW results in welds with superior mechanical properties, ensuring strong and durable joints that meet stringent performance requirements.
These advantages make FSW an attractive option for manufacturers across various industries, particularly those focused on optimizing production efficiency and product quality.
Typical Uses for FSW panels include:
• Ship hulls and superstructure
• Elevator shaft and stair tower walls
• External walls, roofs, rain sheds for large ship buildings
• Modules
• Ribbed deck, hoarding, roof